Setting up a warehouse for your business can feel like a huge milestone. Even when some companies get their warehouse set up correctly from the beginning, you may still need to wait to start. And that’s normal.
Because when you first start your business, you can’t always invest in everything right off the bat. To successfully set up a warehouse, it’s crucial to plan.
It is much more common for businesses to start small, often working from home initially, before they find suitable premises.
Yet, when the time comes for you to invest in your first warehouse, it can be an exciting prospect. If you’re in this situation, you may be wondering exactly what you need to do to get set up.
In this blog post, we’ll explore the steps required to set up a warehouse. Understanding how to set up a warehouse effectively can streamline your operations and enhance productivity.
Table of Contents
Your Warehouse Set Up Checklist
1. Choose The Right Location To Set Up A Warehouse
To begin your warehouse planning, ensure that you select the ideal location for your new warehouse.
This can often be extremely important, as you may need to be in the correct location to access shipping facilities or for staff to be able to come and work for you.
However, it’s much less so in comparison to having a shopfront where you are looking to get footfall.
2. Set A Budget to Set Up A Warehouse for Your Small Business
The next step is to ensure that you have a budget in place for this as well. After all, you need to know how much you can afford to spend each month on renting warehouse space.
Then, you can look for options that are within that range in your warehouse setup process.
Determining a budget to set up a warehouse begins by listing all expected costs. Start with the basics: building or lease expenses, utilities, insurance, and property taxes.
Don’t forget the one-time setup costs, like shelving, security, Wi-Fi, and signage. Count your staff needs and factor in salaries, training, and uniforms.
Running a warehouse entails ongoing expenses, including repairs and cleaning, as well as equipment upkeep and pest control. Build in a buffer for the unexpected. Finally, compare your numbers with local averages and consult with vendors to verify your estimates.
Staying organized helps you avoid surprises and keeps your project on track from day one. For helpful worksheets and checklists, check out Small Biz Tipster’s resources to keep your planning process stress-free and straightforward.
How to Set Up a Warehouse Budget for Your New Warehouse
Start by listing every expense to set up a warehouse—don’t guess or skip on the details. Break your budget into main categories: building or lease costs, equipment, technology, staffing, utilities, and insurance. For building or leasing, include deposits, rent, and any renovation costs.
For equipment, consider items such as shelves, pallets, forklifts, and safety gear. For technology, add up costs for inventory software, computers, and scanners. Staffing covers hiring, training, payroll taxes, and benefits.
Utilities mean power, water, internet, and security systems. Insurance protects your business and property. Add a small buffer (approximately 10% extra) for unexpected costs, as things rarely go exactly as planned.
Use a spreadsheet or budgeting app to track spending live to set up a warehouse on budget. Review quotes, check with vendors, and compare prices. Once you’ve set precise numbers, stick to them.
Set regular check-ins to adjust as needed, as cost changes are common in the early months. Need a template? Check out resources like the warehouse budget planner at SCORE to get started.
3. Have Enough Space for Warehouse Set Up Plan
The next step is to determine the amount of space you need for your warehouse setup. You really won’t want to find that you haven’t got enough room for all of your stock and equipment. Be sure to know the square footage you’re working with here.
Figuring out how much space you’ll need in your new warehouse starts with the numbers you already know. Start by listing every type of product you plan to store.
Note the size, amount, and how you’ll stack or shelf each item to set up a warehouse. Measure any special areas you’ll need, like loading docks or workspace for packing orders.
Calculate your total storage footprint, then add extra square footage for aisles and movement (typically 20-30% more than the storage area alone). Don’t forget room for growth if you expect business to pick up soon.
Create a rough sketch or use simple online tools to map it out. If you aren’t sure about the space required for your equipment or staff, it helps to walk through a similar-sized warehouse or consult with your operations team.
Getting this right up front will save you from costly moves or work slowdowns later.
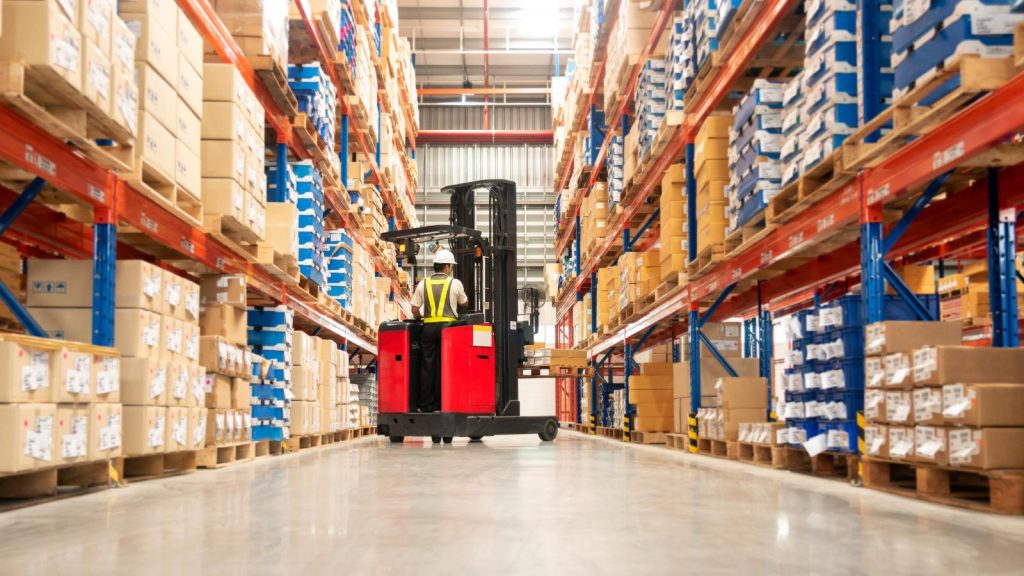
4. Kit It Out to Create A Warehouse
Once you have made your choice, you may need to make some adjustments to the space to prepare it for use. Whether that’s bringing in shelving, recessed can lights, or even setting up an office space and meeting rooms.
Setting up a new warehouse for your small business starts with thoughtful planning and clear goals. First, measure your space and sketch a layout that leaves room for aisles, stocking, and packing. Shelving comes next.
Choose racks that fit your products and allow you to reach your inventory quickly. Label every shelf and set up barcode scanning if possible (this cuts down on lost items and wasted time). Safety matters, so install bright lights, clear signs, and keep fire exits open.
An easy-to-use inventory system (even a simple spreadsheet or software like Sortly) tracks stock and stops you from double-ordering. Purchase sturdy equipment—consider items such as carts, ladders, and packing tables.
Don’t forget break spots for the team. If you keep things organized from the start, your warehouse runs more smoothly and customers receive their orders faster.
5. Settle Into Your New Warehouse
At this stage, all that’s left for you to do is ensure that you get settled in. It’s not always easy to set up shop in a new location, but it’s certainly exciting.
So enjoy it. As you’re finding your bearings, definitely look to make it your warehouse.
Bring in some creature comforts such as photo frames, your favorite coffee mug, and even a bit of music. That way, you’ll be settled into your first warehouse in no time at all.
Don’t forget to add your new location to the local directory listings so you can be found easily online.
6. Can AI Help Me Set Up A Warehouse?
AI can help you set up a warehouse by automating many of the time-consuming parts of the process. You can use AI-powered tools to map out your storage layout, track inventory levels in real time, and spot supply gaps before they slow you down.
Many small business owners utilize simple software with built-in AI features, such as barcode scanning apps or systems that forecast demand based on past sales. These tools often include easy-to-read dashboards that keep you updated without extra work.
You won’t need a large IT team or a big budget. AI can suggest the best storage spots for fast-moving products, help you spot waste, and even send alerts when you’re running low on key items.
To get started, look for warehouse management software that offers strong customer support, a simple setup process, and positive reviews from other small business owners. Give it a try and see how much time and stress you can save.
Conclusion: Set Up A Warehouse
In conclusion, setting up a warehouse for the first time doesn’t have to be daunting. Remember the essentials: strategic layout planning, efficient space utilization, and safety protocols.
Start with these foundational steps, and you’ll build a robust operation. Ready to transform your space into a buzzing hub? Take action today and turn these tips into reality.
Setting Up Your First Warehouse: FAQs
What are the key factors to consider when choosing a warehouse location?
Consider proximity to suppliers and customers, transportation access, zoning laws, and cost. The correct location minimizes delivery times and reduces shipping costs.
How should I determine the layout of my warehouse?
Start by analyzing your workflow. Consider storage needs, equipment, processes, and safety regulations. Aim for efficiency in movement and storage.
What are the essential warehouse equipment and tools I need?
Basic equipment includes forklifts, pallet jacks, shelving units, and conveyors. Assess your specific needs based on volume and type of goods.
How can I ensure safety in my warehouse?
Implement regular safety training, utilize clear signage, maintain equipment, and ensure adherence to safety standards. Regularly review and update safety protocols.
How do I manage inventory effectively?
Utilize an inventory management system to monitor stock levels, track orders, and manage deliveries. Implement a system for regular stock audits to avoid discrepancies.
How can technology improve warehouse operations?
Invest in technology like warehouse management systems (WMS), automation, and barcode scanning. These tools enhance accuracy and efficiency.
What are some cost-saving tips to set up a warehouse?
Buy equipment secondhand, optimize space to reduce rent, and negotiate supplier contracts. Implement energy-efficient practices to reduce utility costs.
How do I handle the logistics of my warehouse?
Coordinate with transport providers, streamline goods receipt and dispatch processes, and plan for peak times. Use software to track shipments and deliveries.
What are the legal requirements for setting up a warehouse?
Check local zoning laws, obtain the necessary permits, and comply with all relevant health and safety standards. Consult a legal expert for specific compliance issues.
How can I future-proof my warehouse setup?
Design a flexible layout, invest in scalable technology, and stay informed about industry trends to ensure long-term success. Regularly review operations to identify areas for improvement.